Make radiant fit the house; don’t change the house to fit the radiant
There are many ways to adjust and fine-tune a system’s design.
By Dave Holdorf
One of the greatest marvels of hydronics — and radiant as a subset of it — is its inherent flexibility.
I’ve seen so many different websites, chat boards, and postings out there that refer to and ask about the best type of radiant to install in a house. What it really comes down to is the design.
In essence, a home’s design tells us the temperature of water that we need in the house, how much tubing we need, proper spacing of the tubing, and so many other factors that come into play.
This may stir some controversy, as I know many trade pros have their preferred methods of installing radiant heating. Yet, the importance of this message is to remember the goal: getting radiant installed in the home.
At its simplest: make the radiant fit the house; don’t change the house to fit the radiant. There’s a lot in that sentence to interpret.
One of the real marvels to hydronics — and radiant as a subset of it — is its inherent flexibility. There are so many ways to adjust and fine-tune a system’s design.
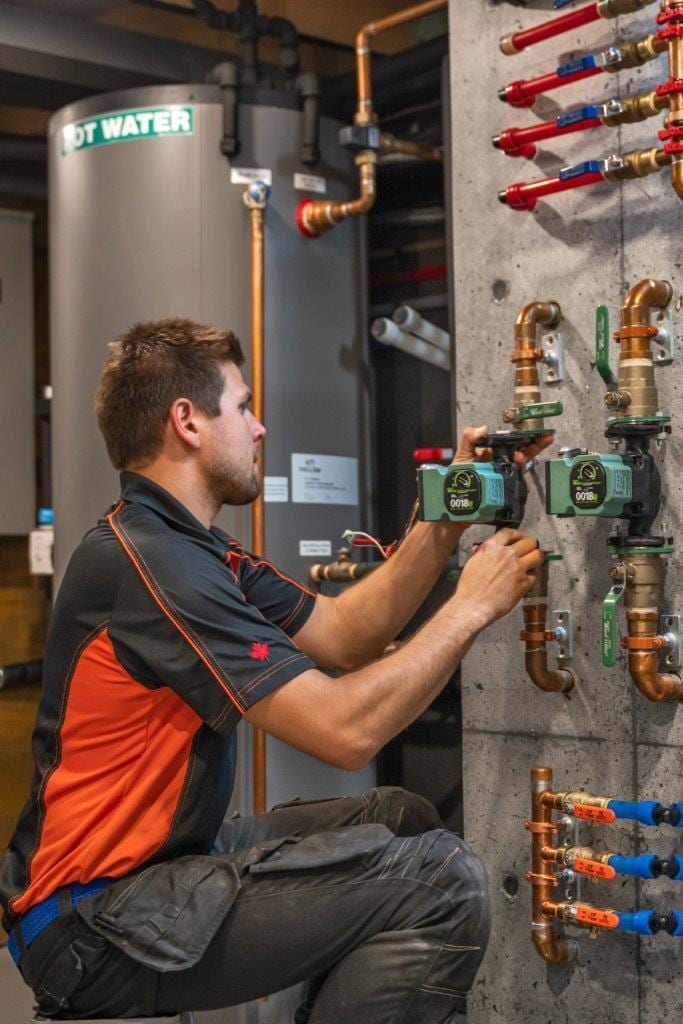
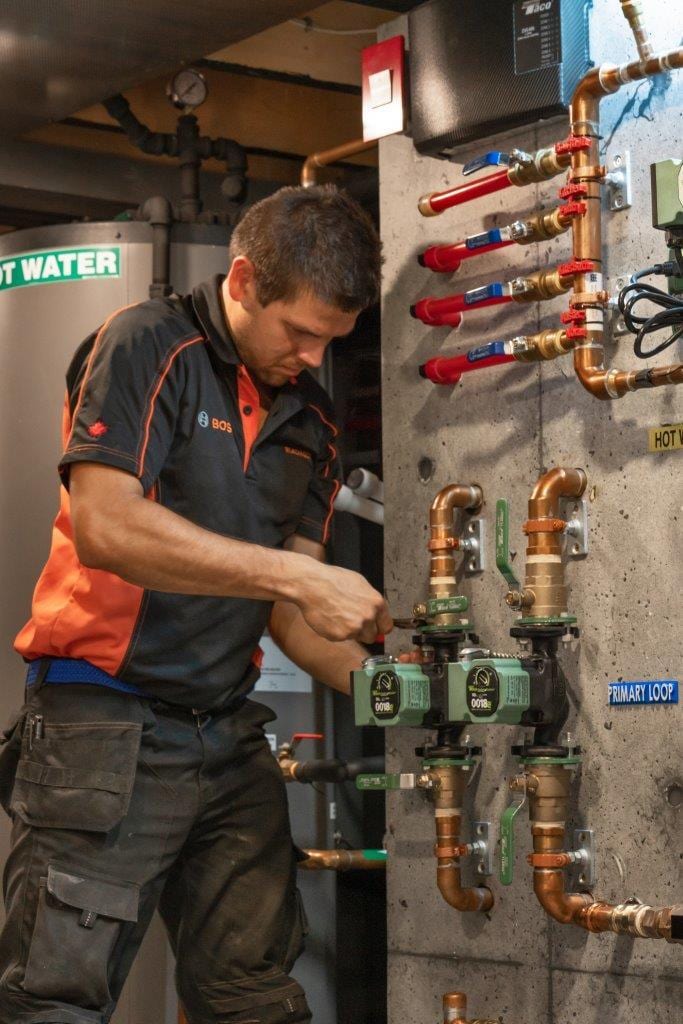
When questions arise about the best way to install radiant heating, there are invariably many responses — many offering the virtues of one methodology or another, along with references to a frustratingly broad list of products sure to guarantee success.
Keep it simple
When thinking about a radiant heating system for a home, the variations, options and the many different types of installation methods can be mind-boggling. And though we’ll keep that in mind, I’d like to offer this to help you stay on course: regardless of the options, always do your best to simplify each facet of the job for all parties involved, and when it comes to the mechanical room — the same message applies.
When it comes to radiant heating of floors (walls, ceiling, or higher-temp panels), keep in mind that the goal of the customer is to have radiant.
I frequently participate in forums and discussions about this, and visit many different sources of education about this very topic. When questions arise about the best way to install radiant heating, there are invariably many responses — many offering the virtues of one methodology or another, along with references to a frustratingly broad list of products sure to guarantee success.
But not here.
For example, there are lightweight concrete devotees who’ll assure you that their method is the best way to heat a home, in addition to providing family unity and happiness. Sure, a thin overpour offers efficient distribution of heat, and retains heat beautifully. But, can the house bear the additional weight from that 1-1/2” pour? There’s also the need for double-plating during the home’s framing. Could there also be floor height or other construction issues with doors, flooring height, and trim?
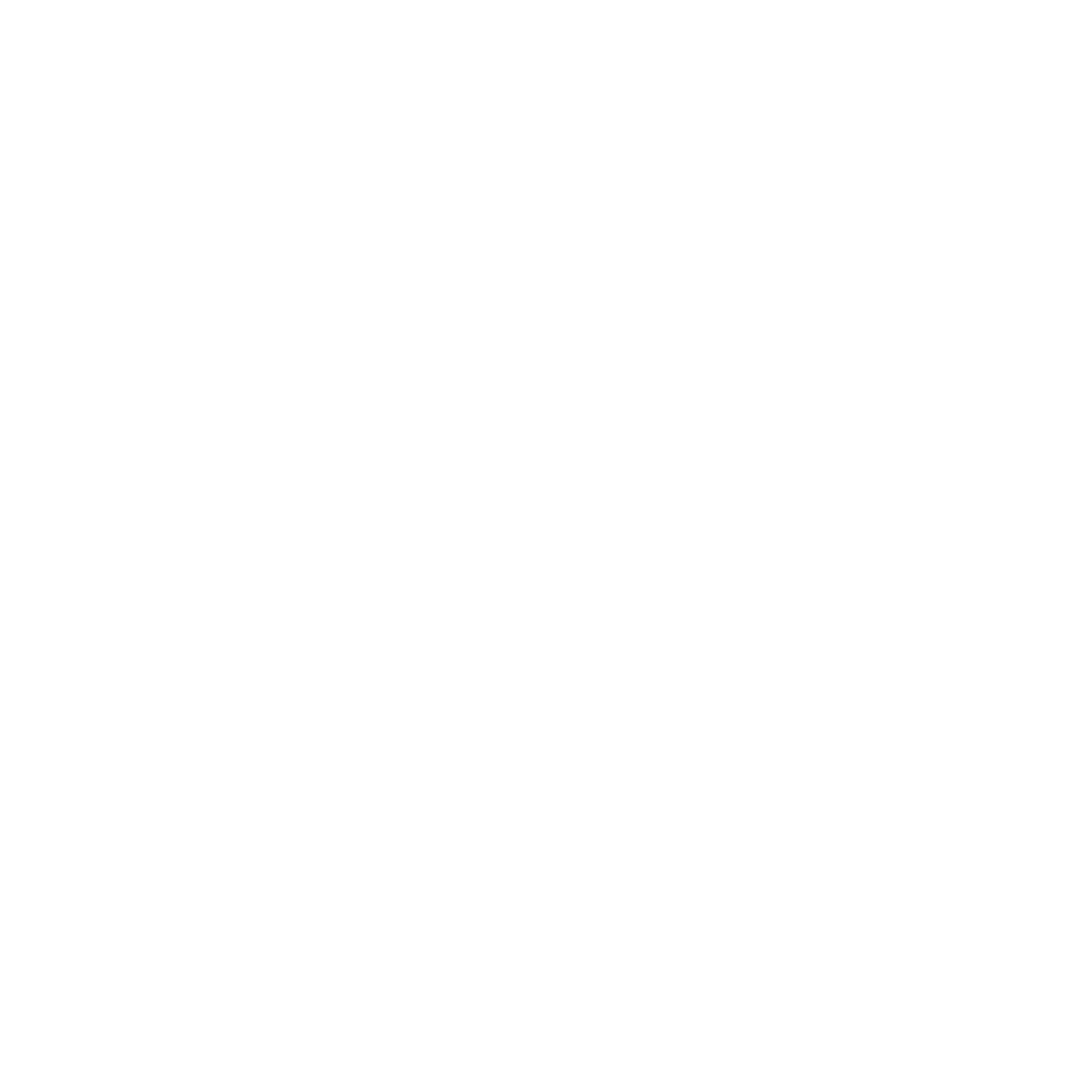
The greater the distribution of heat (or, some might say: the greater the ability of the tubing to warm the floor above), the lower the water temperature. And, keep in mind: the lower the temperature, the better.
The “easier” installation methods, along with the complication of different finished floor coverings — that always influence the rates of heat loss — may, in fact, add complication. The homeowner’s desire for shag carpet (and heavy padding) in one area and, nearby, tile or stone flooring point this out. The carpeted floor will require much higher temperature delivery to achieve the same heat output when compared to those spaces with hard floor surfaces.
So, how many different temperatures will the mechanical room be called on to accommodate? Making this happen has a major impact in the mechanical space: to accomplish a large spread in desired water temperatures, the installer must now have at least two different mixing valves, circulators, manifolds and zones.
All about retrofit
Let’s now look at popular underfloor applications used for retrofit projects. The three methods of getting a radiant floor heating system installed is suspended tube, tubes with heat emission plates and tubes with heavy extruded plates.
Each installation method has its pros and cons, but the biggest difference between them is the water temperature requirement. The greater the distribution of heat (or, some might say: the greater the ability of the tubing to warm the floor above), the lower the water temperature. And, keep in mind: the lower the temperature, the better.
Close to home
I’d now like to offer you a real-world example: the second floor of my own home. Initially, I thought I’d combine radiant panel baseboard with suspended tube radiant for the floors in each room.
The radiant panel baseboard was going to be controlled by thermostats in each room. But the radiant floor heating wasn’t going to be controlled by thermostats, but rather by the outdoor responsive system.
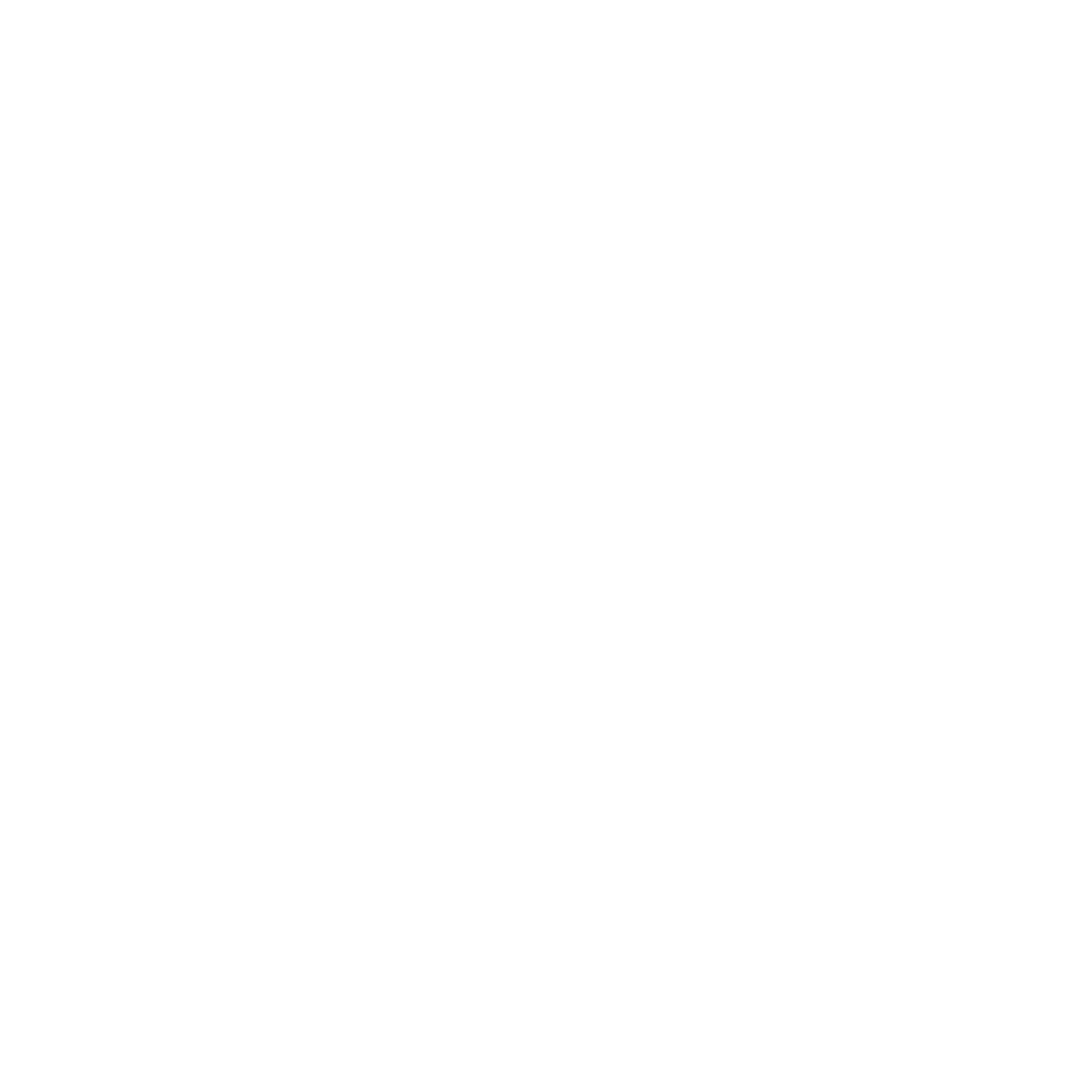
Taco’s zone valve controls work with 2, 3, or 4-Wire zone valves and feature front diagnostic lights, switchable priority, built-in priority protection and simplified wiring.
Initially, these spaces called for rather expensive, heavy-duty heat emission plates, but I did the heat loss and knew I could accomplish it without them. I could save on cost, and the time required to put them in.
However, construction changes called for the use of steel beams rather than new joists — so it would be difficult to run supply and return pipes from the boiler room to the remote spaces where manifolds would’ve been located.
And the second floor would have required two temperatures: high temperature for the radiant panel baseboard, and lower temperature for the radiant floor system.
This would have meant two remote manifold locations and two sets of pipes back and forth from the mechanical room. Now, you might say that this was needed because the design is the design and, after all, the design rules.
But, I really preferred to save money and material by not using underfloor plates for the radiant floor system.
After a lot of thought about the design, the labor and the materials, the best solution was to adjust the underfloor system by adding plates to rooms with a high heat loss and high R-value finished floor coverings, and to stay with my plan to use simple, suspended tubing for the rooms with low heat loss and low R-value for the floors while also eliminating the radiant baseboard.
I couldn’t change the spacing of the underfloor system due to the home’s old joists: they dictated spacing at 8 inches on center. But, what I could do would be to change how the radiant would be installed from below the floor.
By changing the design to fit the house, my installation of the boiler room components became much easier, and less expensive.
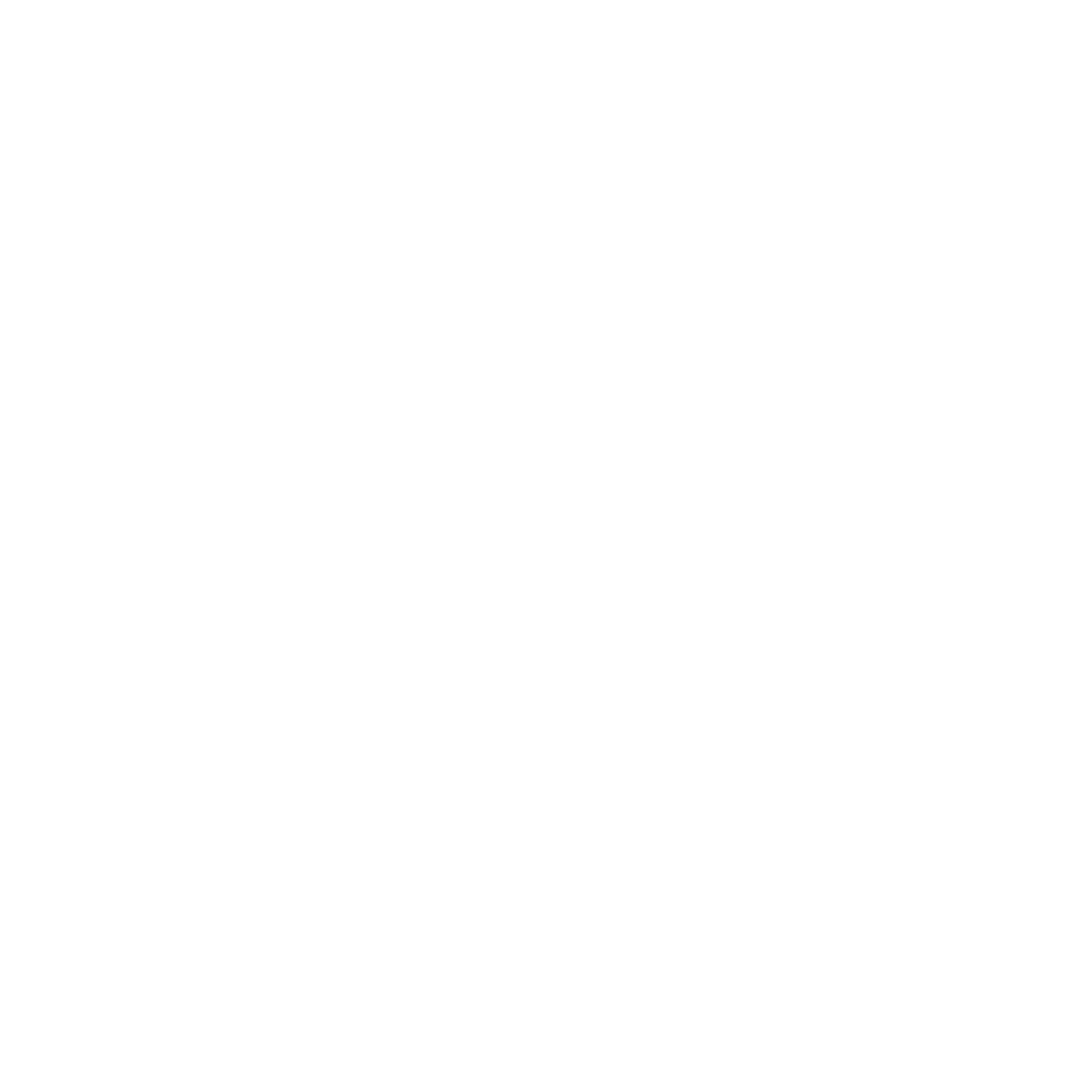
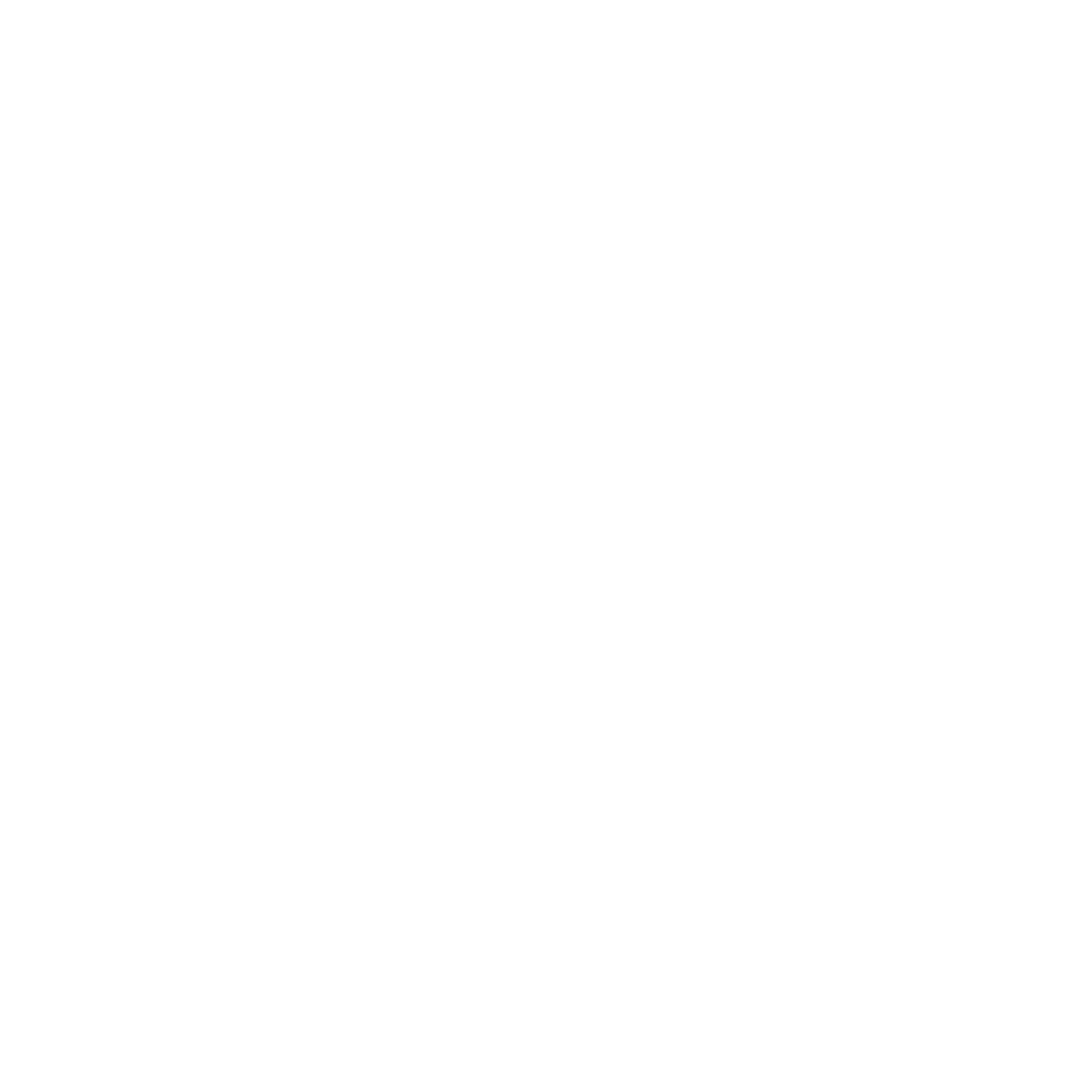
Taco's zone controllers can be monitored via the Taco Comfort app.