The consistency of change
Wait, you’re telling me the homeowner wants a change to the radiant design?
By Kolyn Marshall
Job site changes are inevitable, but flexibility is one of the many advantages hydronic radiant systems have over other types of heating.
There’s a familiar saying that often rings true: the only constant in the world is change.
Radiant installers deal routinely with changes, many of which seem to go unnoticed. These are changes caused by factors outside their awareness or sometimes control.
Below, I’ll explore some of these left-field changes, implications and what can be done in response.
Uh-oh; change-order
First is the dreaded dimensional change. A room or even a floor rarely goes in as specified on the blueprints. For instance, what happens when the GC responds to the homeowner’s mid-stream demand to enlarge the kitchen, or to reduce the size of a sunroom?
Most likely, changes like these influence the coverage area of a given zone. Let’s say the sunroom, for instance, was 400 square feet, but the dimensional change now reduces it to 350.
Typically, the tubing and manifolds are already on site, and the original design called for tubing installed at eight inches on center (an underfloor application). To determine how much tubing is needed, one takes the area and multiplies it by its corresponding correction factor, in this case 1.65.
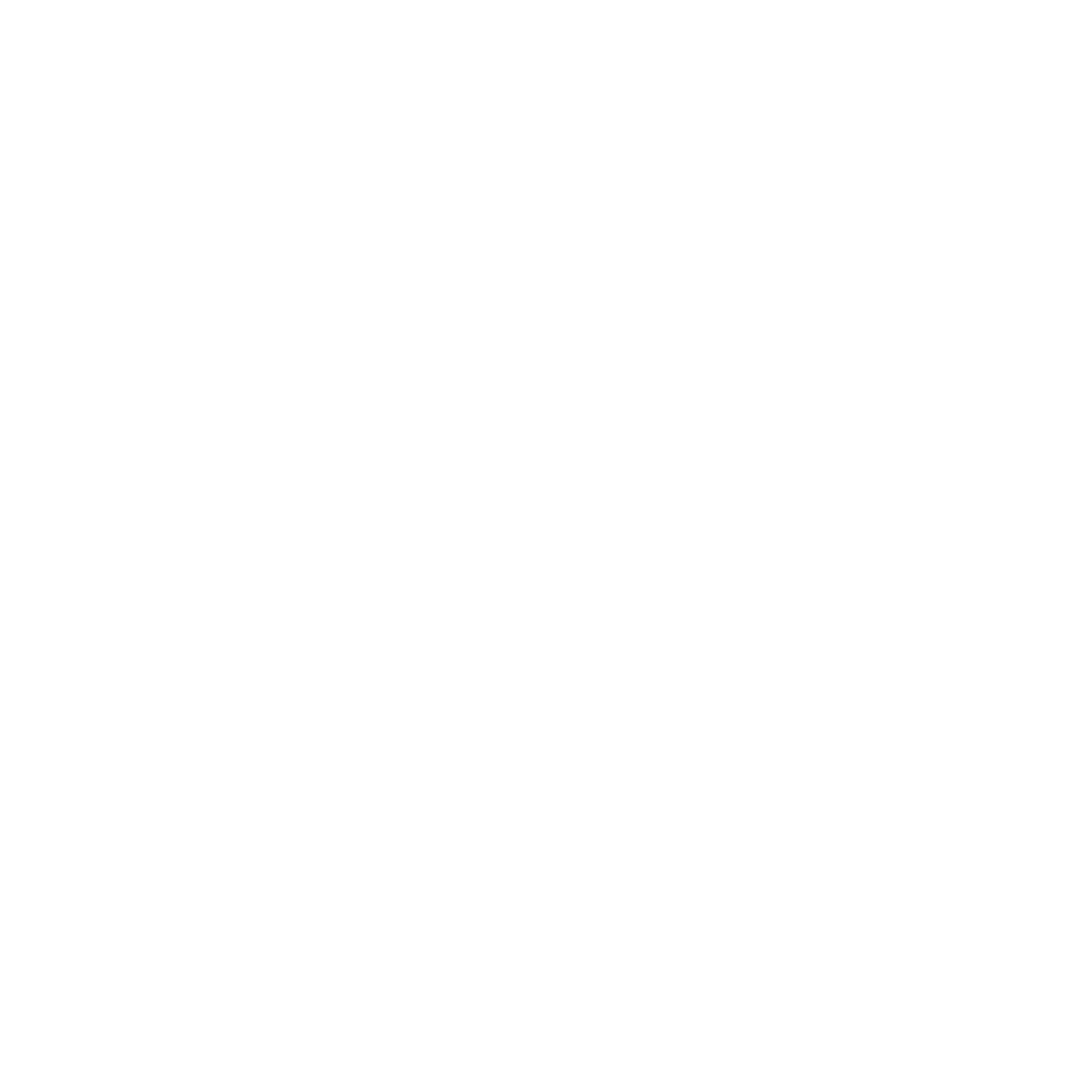
To cover the area as originally specified, we needed 660 feet of tubing. Dividing this amount in half is 330 feet, leaving us with a longer-than-standard circuit length. So, we’ll divide the amount into thirds (660/3 = 220) and add 5 feet to accommodate some extra to transition to manifolds. This gives us three circuits at 225 feet.
The new area is 350 square feet. 350 x 1.65 = 578. With manifolds on site we want to use the same number of circuits, in this case three, making each circuit (578/3 +5 = 198 feet).
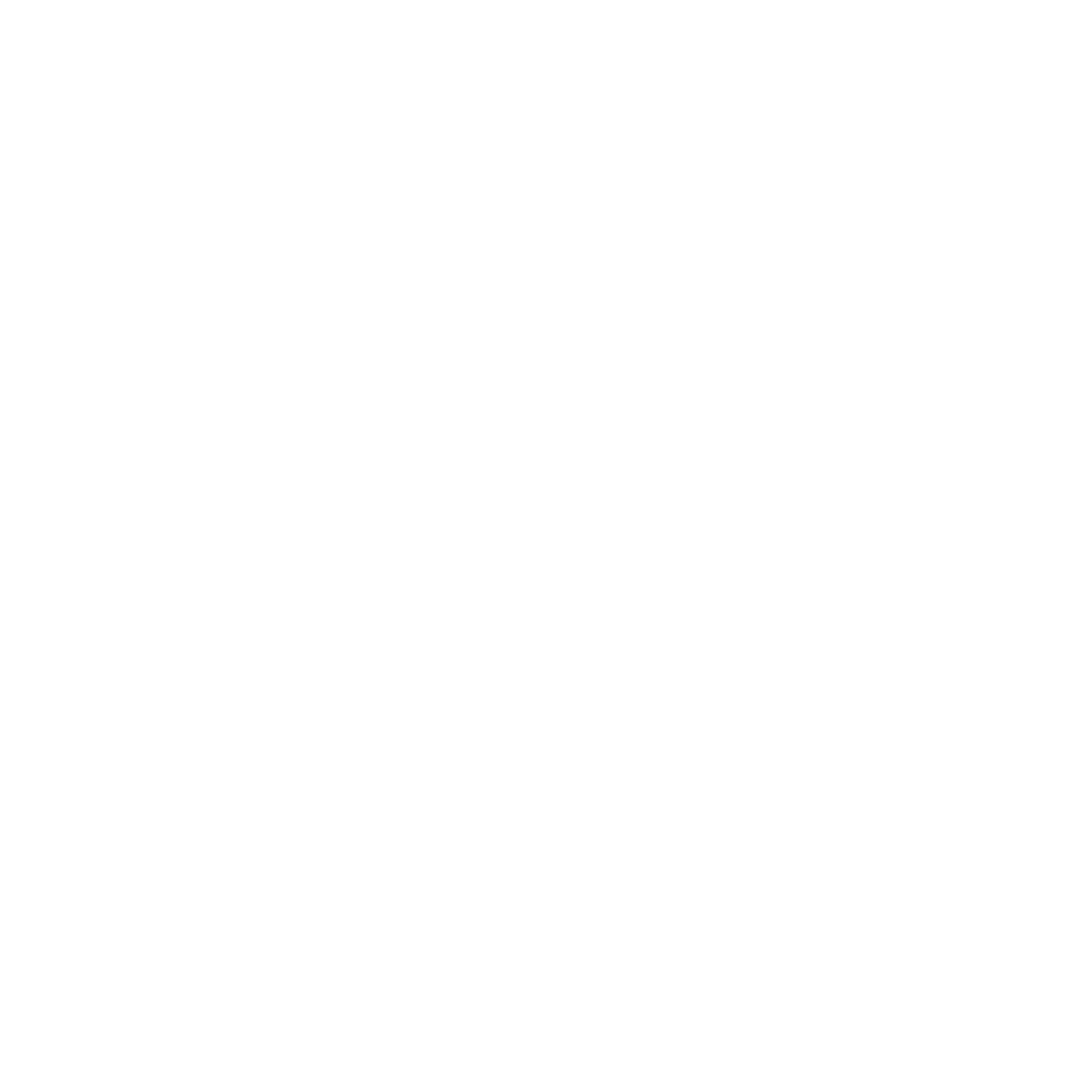
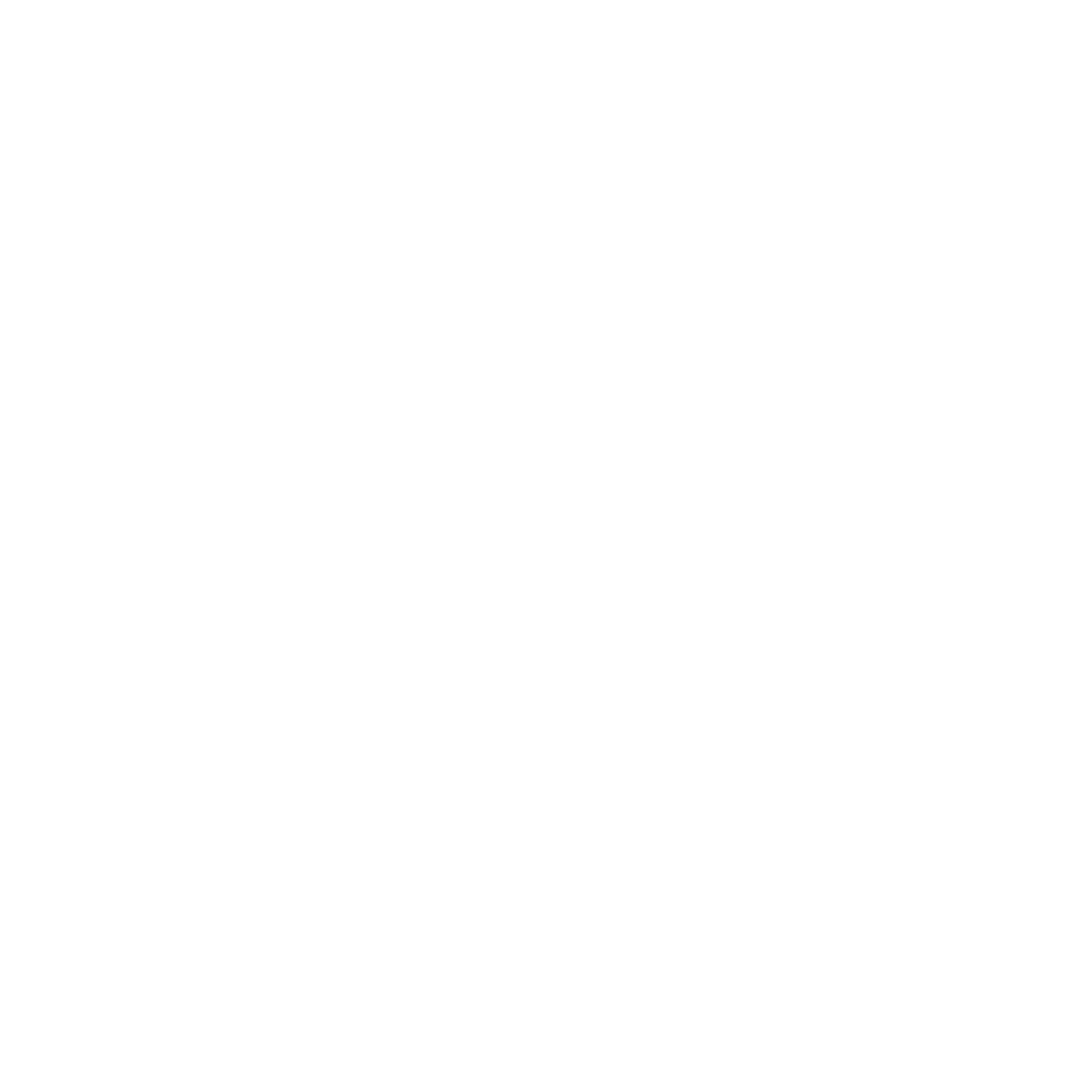
Slab applications for radiant heat are pretty common. There's a bit more flexibility with slab applications than with under-floor systems.
Since the total amount of pipe needed was under 600 feet, it’s possible to divide the amount into 290 foot runs. The issue with this is: it will require each circuit to have more individual flow at longer runs, which can result in a slightly higher head pressure. It also means having to cap the now extra port on the manifold. It’s easier to keep the number of circuits to match the manifold.
A game of inches
Slab applications for radiant heat are pretty common. There’s a bit more flexibility with slab applications than with under-floor systems. The tubing is unhindered by joists and can be placed at virtually any spacing. Although spacing is important, depth of the tubing below the surface of the slab has its own implications.
Most systems are designed with a tubing depth of two inches, approximately in the middle of the slab. To achieve this depth, most installers use chairs, or lifts, to position the rewire/rebar at a specific depth.
In reality, most concrete installers simply lift the rewire up as they poor to a depth and move on. Although this works in theory, what generally happens is that, as they lift, they also step… and the rewire is pushed down toward the bottom of the slab.
Or, the installation is changed to stapling the tubing down to the insulation board under the slab. Either way, the tubing is deeper in the concrete than initially anticipated.
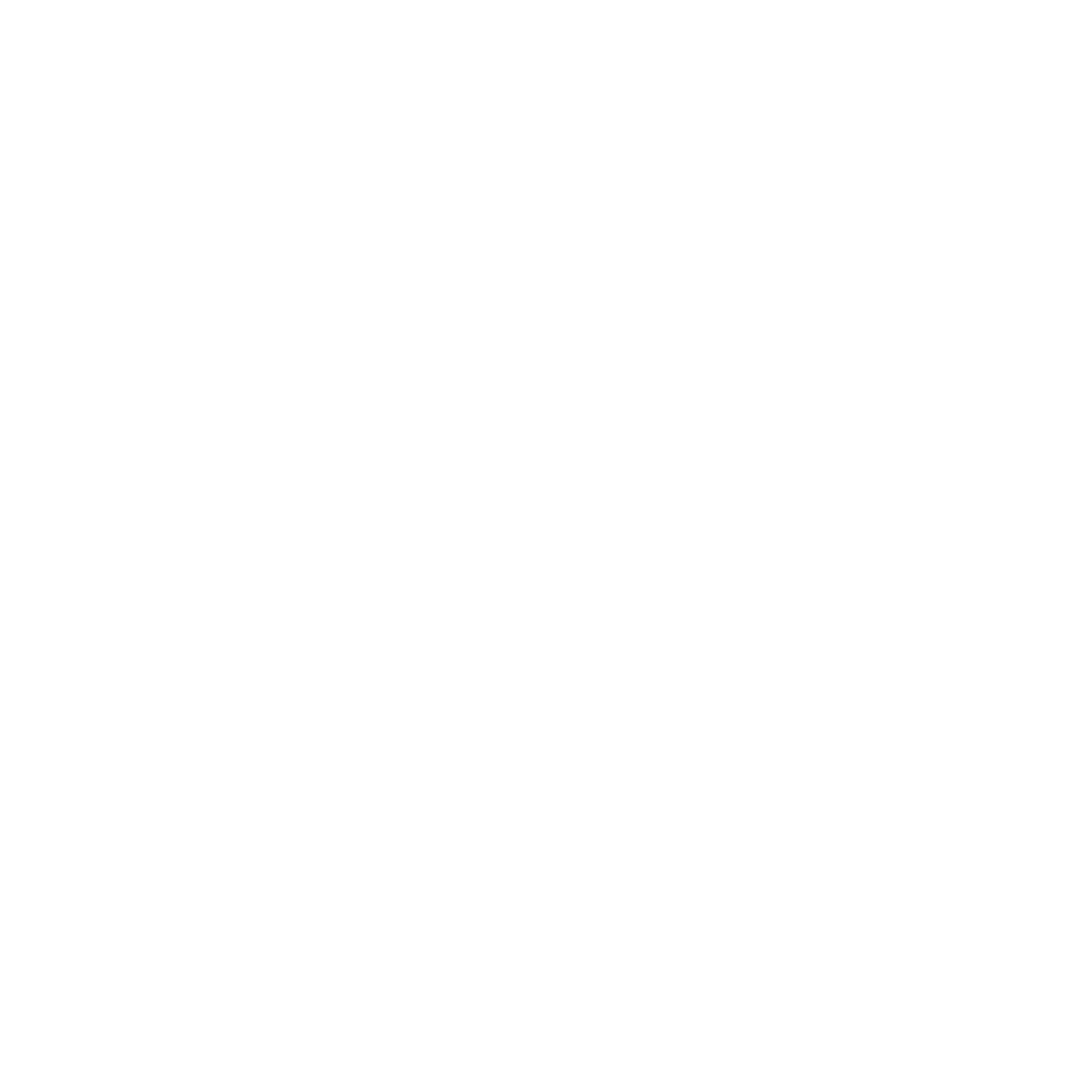
Most radiant heating systems are designed around a 20° Delta T (∆) — the temperature difference between supply and return.
What does this extra depth mean for system design? The material placed over the top of the tubing directly impacts the total R-value above the tubing. This R-value, or thermal resistance, determines what the fluid temperature needs to be. The higher the resistance, the higher the fluid temperature (for a set tube spacing). Deeper tubing means higher supply temperatures.
Floor coverings are another factor that easily impact the R-valve above the tubing. Homeowners frequently change floor coverings with little or no regard for the impact on the radiant floor system. It could be a design calling for tile, but was switched to hardwood or — worse — carpet and padding. If the R-value above the tubing increases, then the supply fluid temperature needs to increase as well.
The cost of saving
Imagine a residence set in the mountains, positioned to overlook a luscious green valley. The home is designed with a great room with high ceilings and one wall of glass that looks out over the mountain range. The plans call for Argon filled Low-E glass windows with an R-value of 4.2.
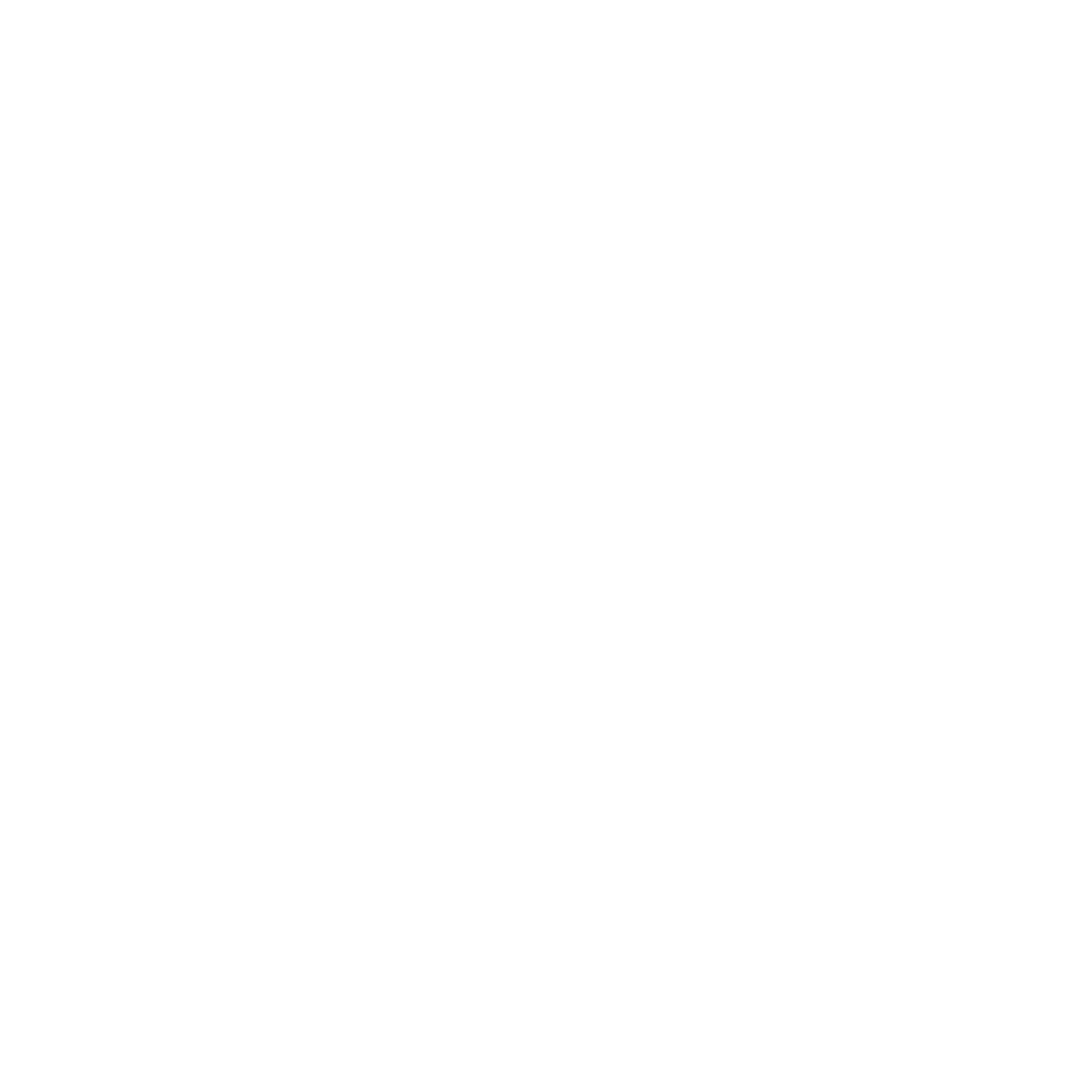
To deliver Btu to a space requires the floor surface temperature to be at a given point. To deliver more Btu means the floor temperature has to increase. Like in the previous examples, in order to raise the floor temperature means raising the fluid temperature.
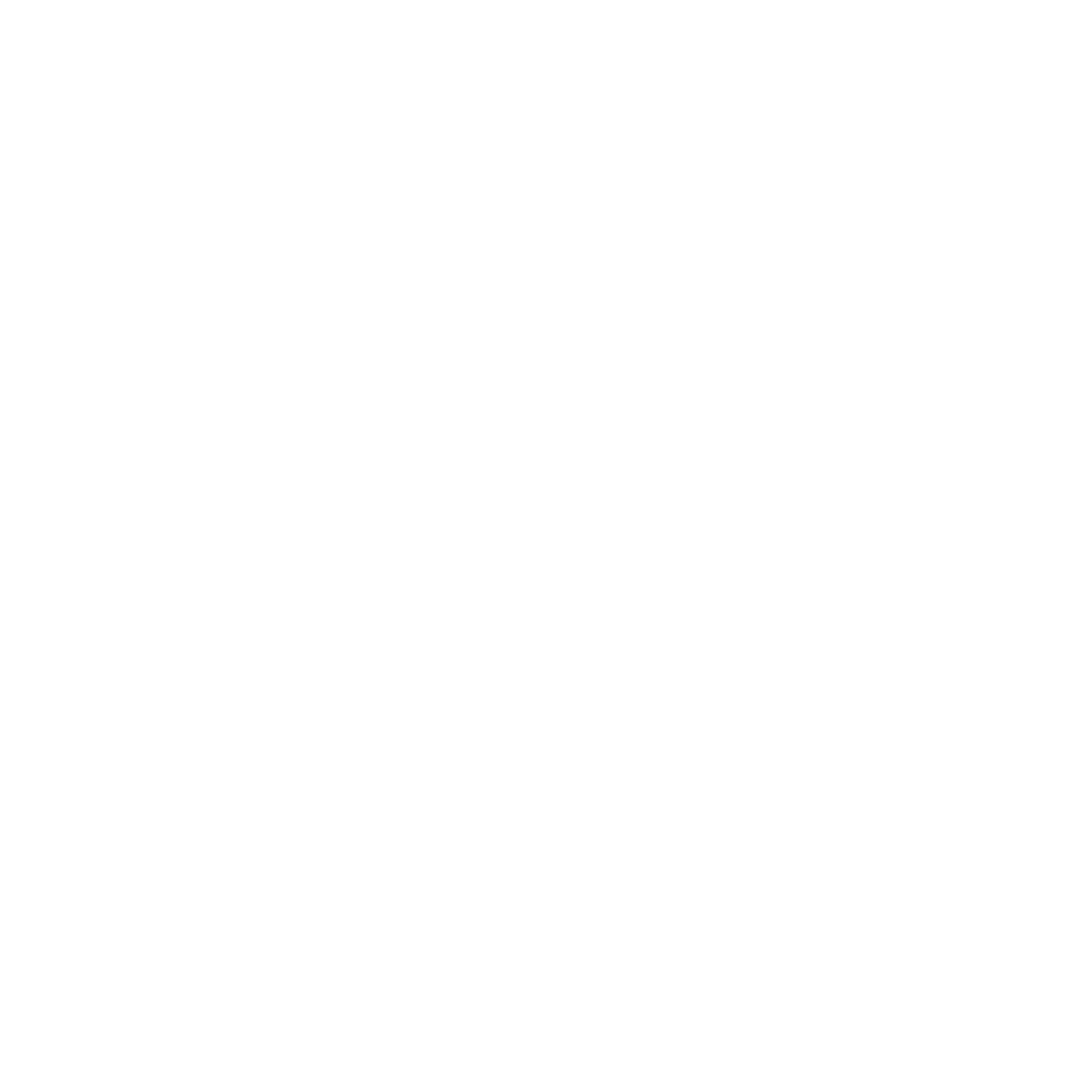
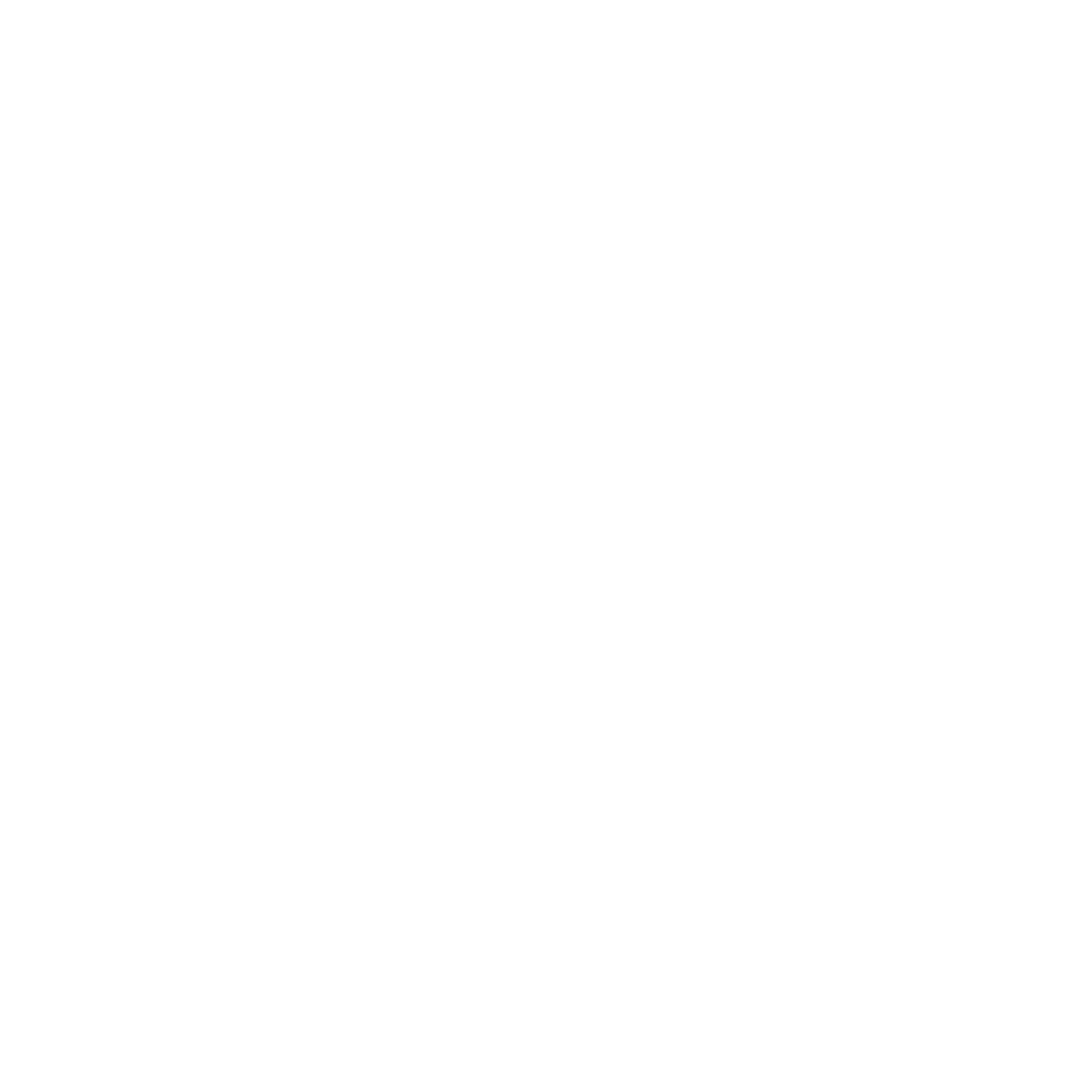
To deliver Btu to a space requires the floor surface temperature to be at a given point. To deliver more Btu means the floor temperature has to increase. Like in the previous examples, in order to raise the floor temperature means raising the fluid temperature.
The radiant designer runs the numbers and comes up with a heat load, pump spec, and fluid temperature. All is good in the world.
Well, not so. As it is with many projects, homeowners are enamored with the ability to make changes. In this case, they consider the cost of Low-E, Argon filled windows and opt to go back to standard R2.4 windows. They fail to notify the radiant installer of this change and no one is the wiser. That is, until winter hits.
In this example we have a large exposed wall with an assumed R-value of 4.2. Reducing the window’s R-value by half dramatically changes the room’s heat loss. In this case, it adds almost 60% more heat loss for the area. How do you compensate for added heat loss?
This challenge is a bit more complicated. It affects the system in several ways. The first is floor temperature. To deliver Btu to a space requires the floor surface temperature to be at a given point. To deliver more Btu means the floor temperature has to increase. Like in the previous examples, in order to raise the floor temperature means raising the fluid temperature.
More Btu also means higher flow rates. We can use the following equation to estimate the necessary flow at a given Btu.
BTU = 500 x Delta T x GPM
Most systems are designed around a 20° Delta T (∆) — the temperature difference between supply and return. This simplifies the equation to Btu = 10,000 x GPM; or, every GPM of flow delivers 10,000 Btu of heat energy.
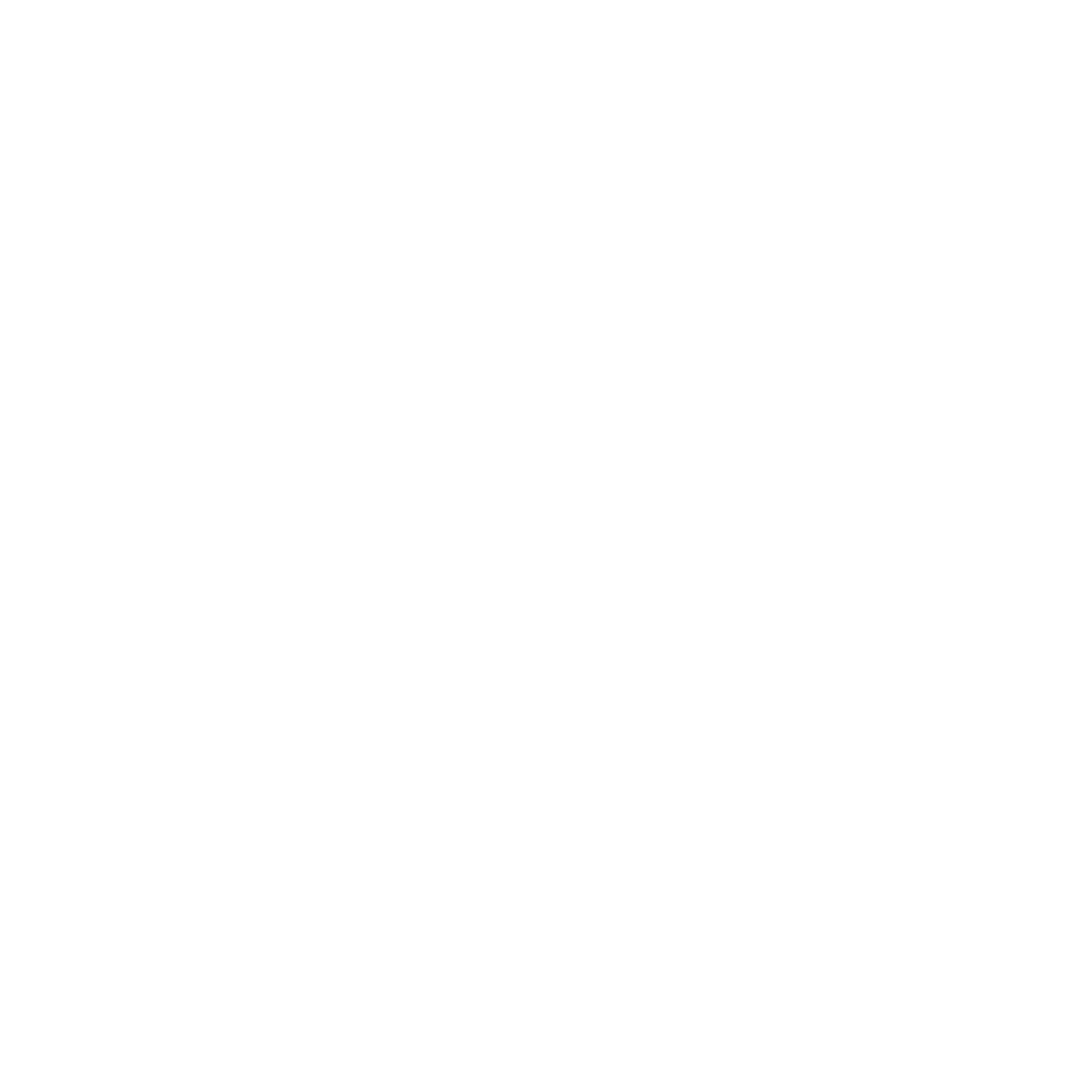
Higher flows will drive a higher pressure drop.
Let’s assume the original design called for 30 Btu/sf with a room size of 600 square feet. In this case the total Btu required is 30 x 600 = 18,000 Btu, or 1.8 GPM.
If we assume the change in windows drove a 60% increase in heat loss, our 30 Btu/sf suddenly becomes 48 Btu/sf.
48 x 600 = 28,800, or almost 3 GPM of flow
To correct this change, our radiant installer would need to increase the fluid temperature and increase the flow. There’s also a chance they may need a larger heat source but in this case the overall change was only 10,000 Btu. Most boilers are somewhat oversized naturally and it’s a rarity for all zones to call for heat simultaneously. Changing the heat source would be a last option once all other system tweaks have been tried.
If the above changes didn’t work, the next tweak would be to reduce the zone’s delta T. As noted below, most systems are designed with a 20°F ∆T. Design software takes this drop to calculate an average floor temperature. Reducing the ∆T from 20° F to 10° F provides a higher average floor temperature at a given supply temperature. It may be possible to get a bit more from the floor by making the temperature more even.
Reducing the Delta T will result in a higher flow rate.
48 x 600 = 28,800
28,800 = 500 x 10 x GPM
GPM = 5.76
Higher flows again will drive a higher pressure drop. Like most things, nothing is free. This option costs a potential change in circulator sizing, too.
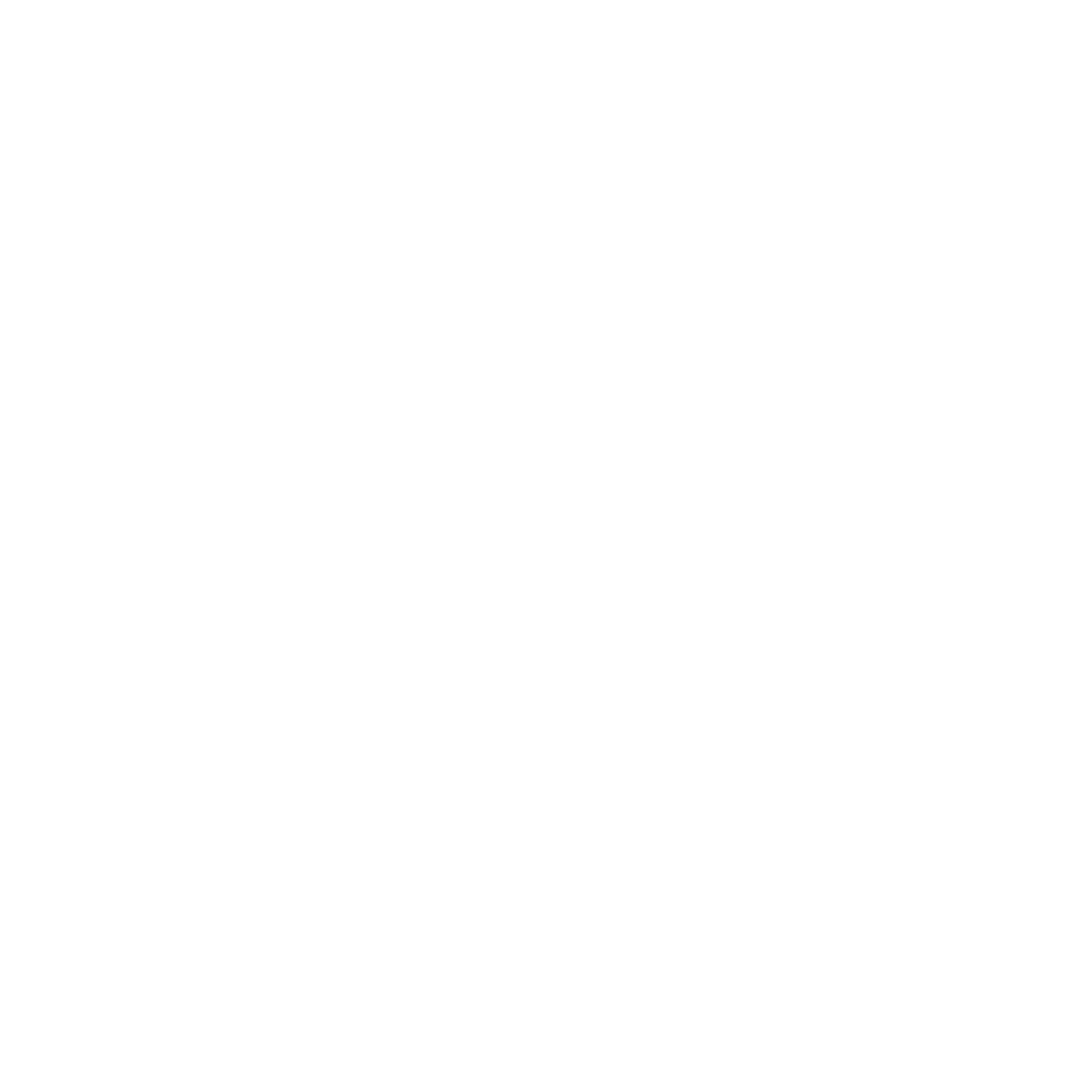
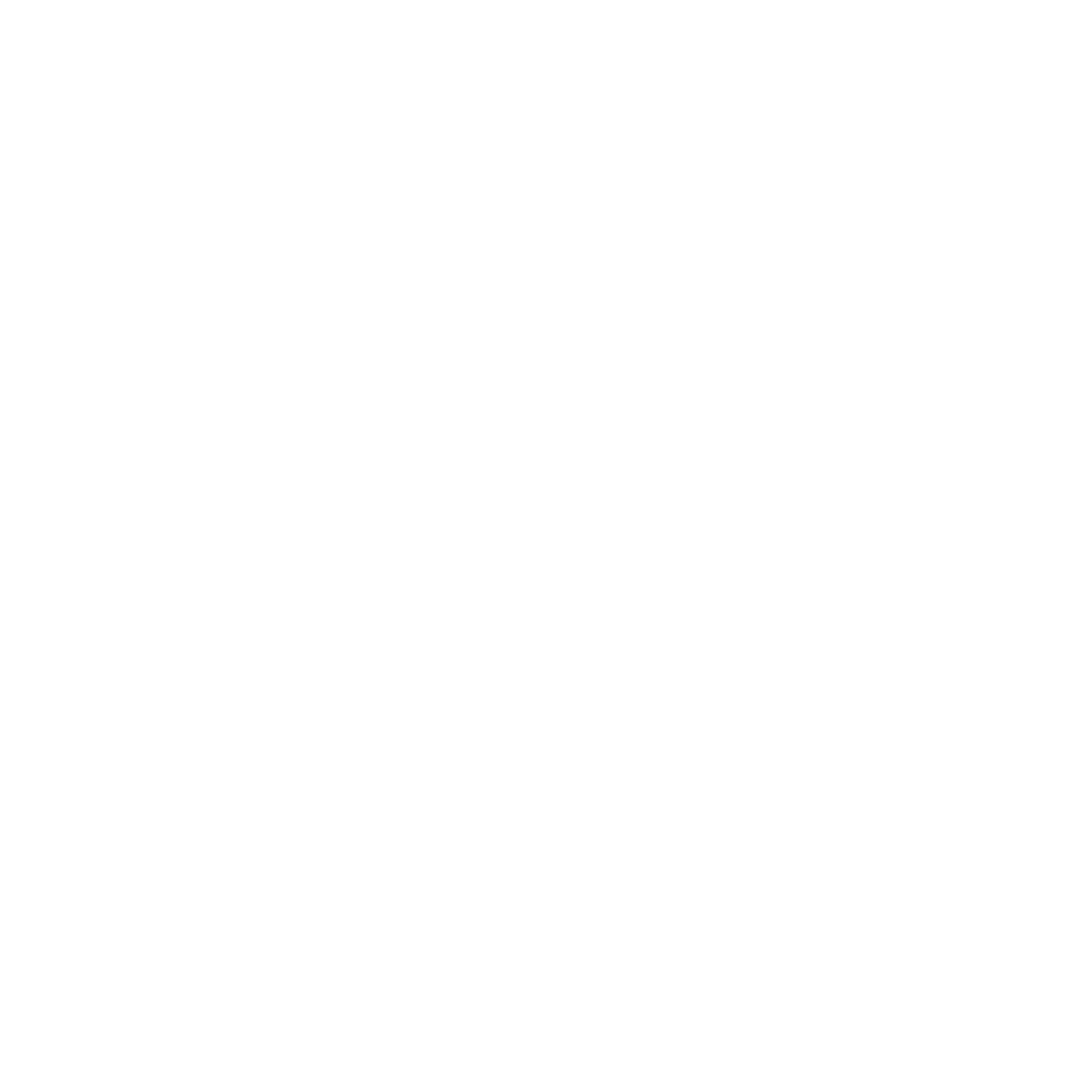
The best thing any installer can do is to learn the why’s behind radiant designs.
Embracing change; not if, but when
Change is inevitable, not a matter of if, but when. Fortunately, there’s no reason to be afraid of job site changes. There are a lot of tweaks one can make to accommodate the call for change and to compensate for it.
Actually, this sort of flexibility is one of the many advantages hydronic radiant systems have over other types of heating. We have a wide range of factors that can be adjusted to provide an even wider range of results.
The best thing any installer can do is to learn the why’s behind radiant designs. The more one understands why a specific tube spacing is used, or how the supply temperature is determined, the better they are at responding to the call for change when it comes.
IMAGES courtesy of Watts Water Technologies